Stowell Concrete Commissions 'State Of The Art' Plant
<strong>STOWELL CONCRETE COMMISSIONS 'STATE OF THE ART' COLUMBIA CPM+60 CONCRETE PRODUCTS PLANT AT THEIR YATTON HQ IN SOMERSET, UK.</strong> With over 60 years of hands-on experience delivering across the UK, Stowell Concrete has carved out a leading position in the industry and continues to grow.
Situated on the edge of Yatton, right in the heart of stunning North Somerset, in the South West of the United Kingdom, Stowell Concrete is an outstanding, fully independent, family-run business specialising in the manufacture of an extensive range of quality concrete products.
With over 60 years of hands-on experience, delivering across the UK, they have carved out a leading position in the industry and continue to grow. Stowell Concrete has earned a very proud and well-deserved reputation for dependable, dedicated service with a careful and uncompromising focus on quality.
A Brief History Of Stowell Concrete
Roger Stowell, who was born in 1939, began what became Stowell Concrete in September 1959, in a field behind the family farmhouse in the village of Kenn, near Clevedon. He was the youngest of four children, unlikely to inherit the farm, so he explored agricultural contracting. He also bought a small block machine with a capacity of five blocks to use when the business was quiet.
Concrete blocks took off, Roger continued investing in his block making equipment rather than his agricultural equipment and when he was confident in his ability at block making, he bought his first land at Yatton in 1968 and moved the block production there. He installed hydraulic wet presses to produce commercial slabs in the yard at Kenn.
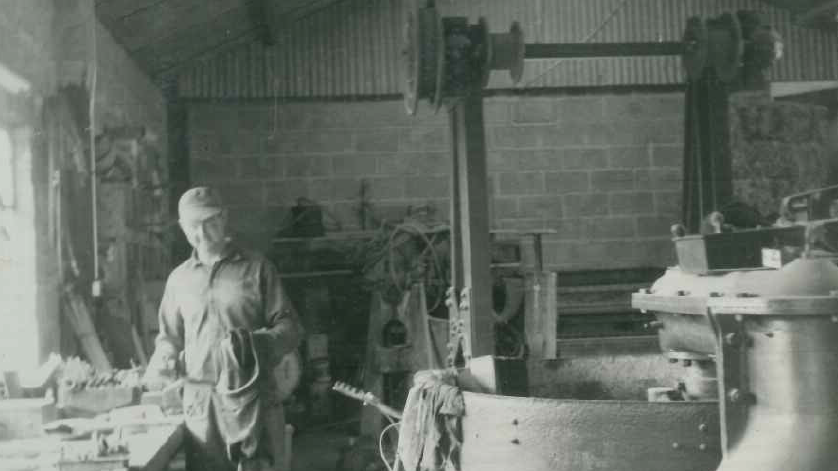
Roger Stowell in the workshop at Kenn (1970) with a mixer being refurbished.
Roger met Margaret Gillard on Clevedon Pier on Easter Monday in 1960, and they were married in 1964. By 1968, they had three children and lived in the old farmhouse with the concrete works behind.
The Holcombe yard was purchased from receivers in 1979 to expand hydraulic wet pressing further, adding kerbs, edgings, channels and T-beams to the product range. The former owners, Bristol Stone and Concrete, had specialised in bespoke concrete products, where Stowell Concrete has always made standard products for stock.
Land adjoining the Yatton works was purchased at every opportunity so that a total of 30 acres is now under their ownership and this has allowed Stowell Concrete to expand the yard fi ve more times over the years. The small Kenn operation, including the head office, was incorporated into the Yatton yard in June 1996.
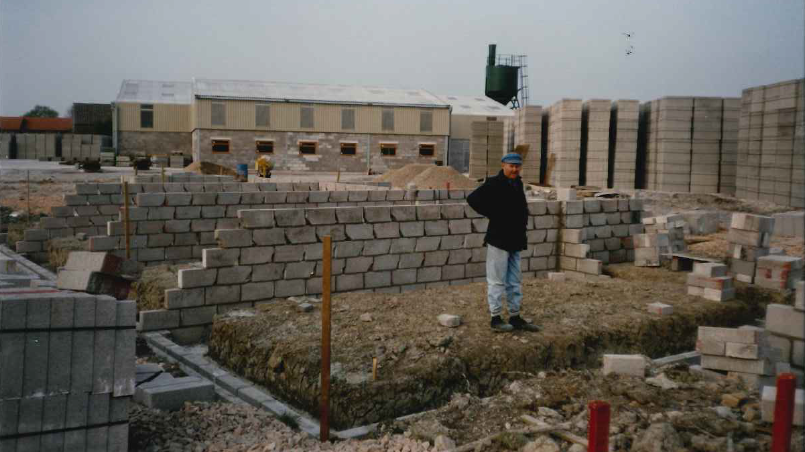
Roger Stowell, standing in the new head office's foundations at Yatton (1995) before moving from Kenn.
In January 1997, Roger died suddenly after developing a heart condition. With the help of a long term and loyal workforce, Margaret and her eldest son Vince, who had been working in the business full time from the age of 17, were able to continue. Vince was promptly appointed as Managing Director.
A small block yard was purchased in Weston-Super-Mare from a competitor in 2001, and 2 years later, an opportunity came up to lease land within Callow Rock Quarry, one of the quarries that still supplies Stowell Concrete with aggregate, so the block production was moved from Weston-Super-Mare.
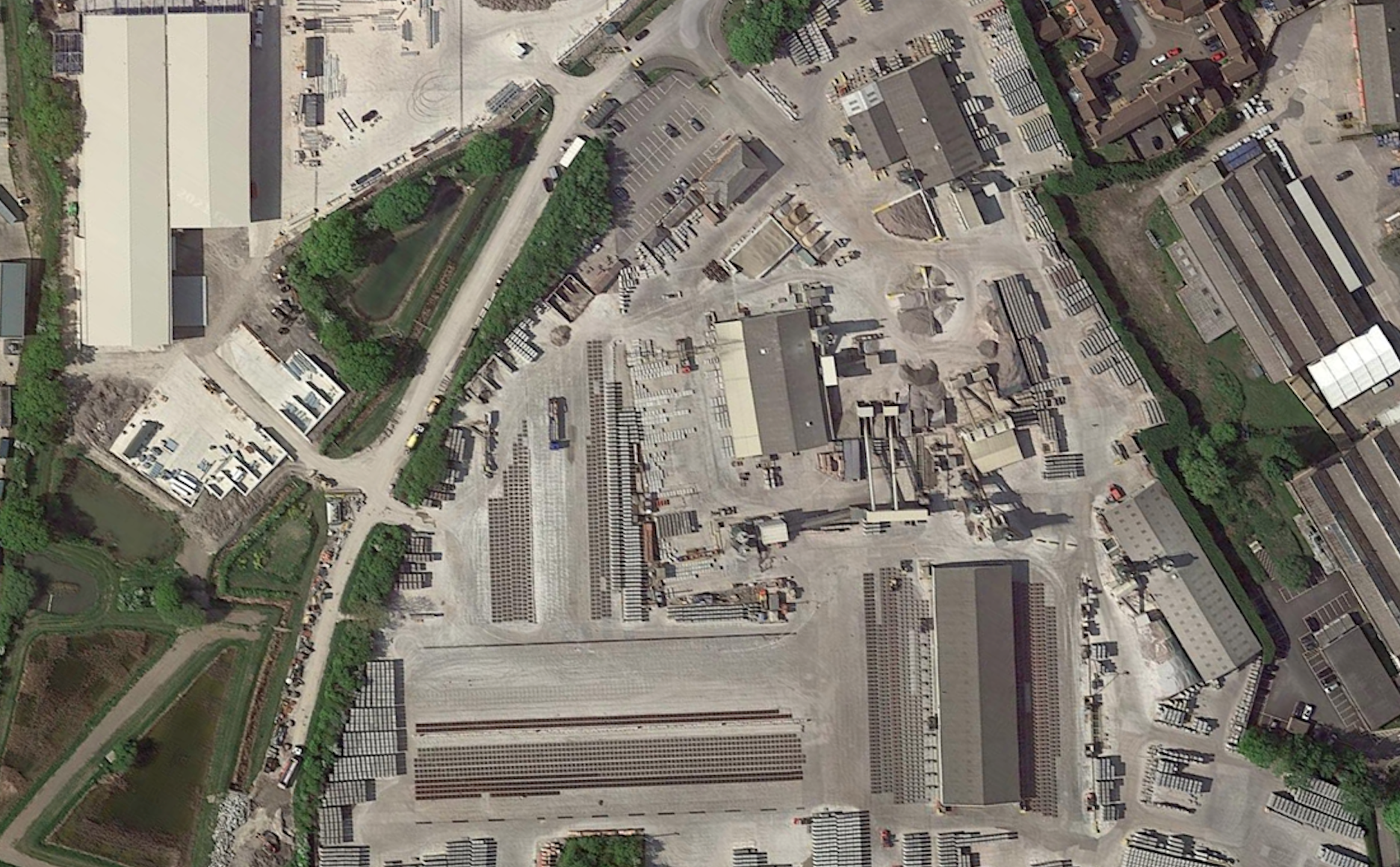
Stowell Concrete: Yatton Head Office & main manufacturing site.
The Beginnings Of A Long-Term Partnership With Columbia
Early in 2019 Vince’s daughter Beth, the eldest of the 3rd Stowell Concrete generation, accompanied her father with senior engineer, Dave Devine and Columbia’s UK sales representative, Stephen Wilson, on a fact-finding trip around North America to look at Columbia production plant versatility, meet the Columbia team and see block machines being made at factory HQ in Vancouver WA.
A Columbia CPM+60 block machine was chosen and soon on order along with all associated batching and mixing plant with handling equipment. Despite the challenges of the COVID-19 pandemic, construction kept on track, and the plant is now up and running, finally utilising all of the available Yatton land.
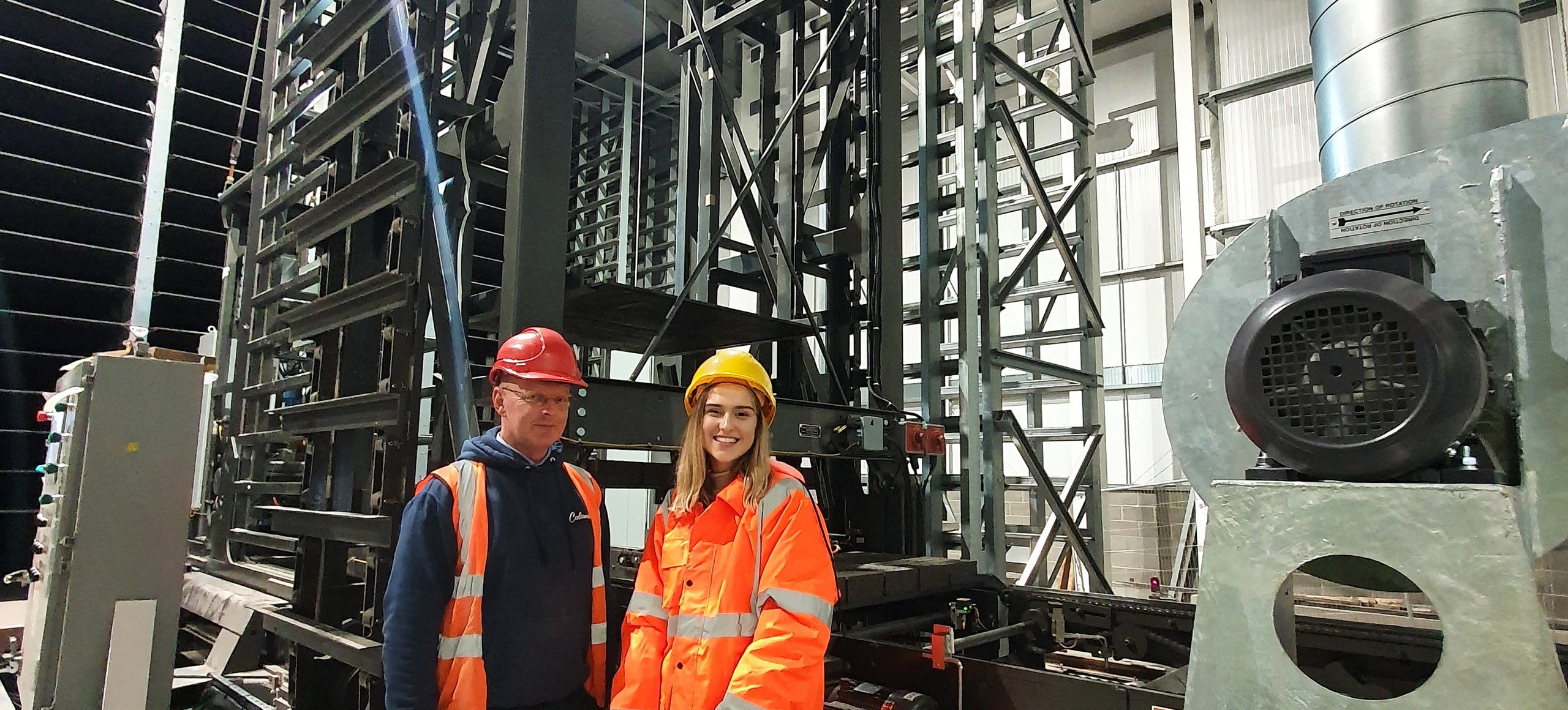
Vince Stowell (Managing Director of Stowell Concrete), with his eldest daughter Beth during the installation of their new Columbia CPM+60 plant (2020).
An Ultra-Modern 'State of the Art' CPM+60 Concrete Products Plant
Stowell Concrete opted for two independent sets of 4 x 40 cubic metre aggregate storage bins with feed to the bins from ground shovel dump hoppers and incline belts to a rotary conveyor. The driver selects a bin from a remote control in the shovel cab, to feed the aggregates to the bins which have high/low-level light indicators. Designed and constructed by Concrete Batching Systems Ltd in Ireland and using weighing and control automation by another Irish firm, Pneutrol International Ltd, each concrete batch is metered onto a weigh belt and conveyed to any one of three dry aggregate holding hoppers over the relative mixers.
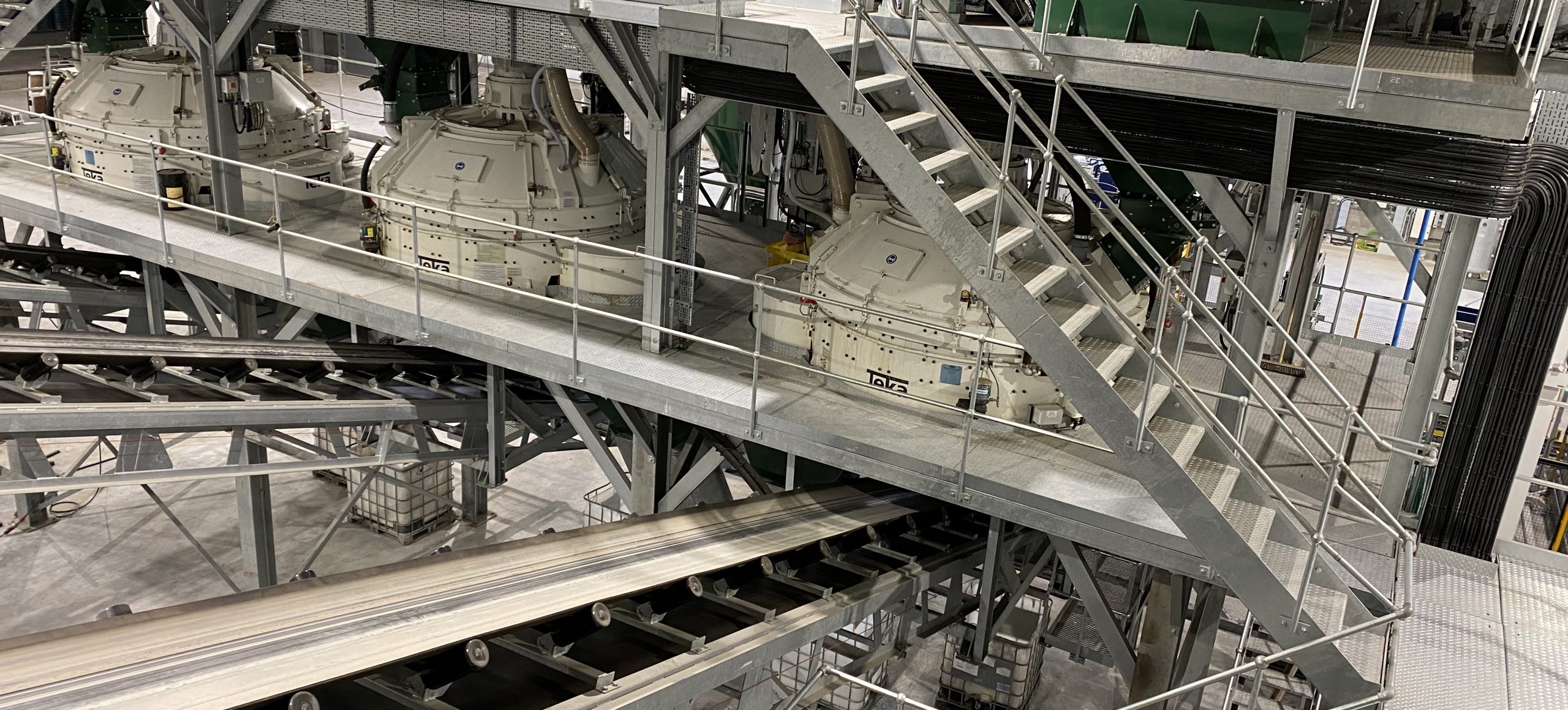
Plant mixer station by Concrete Batching Systems, Ireland.
The moisture quality check of material feeding the Columbia CPM+60 uses the latest Hydronix moisture system with real-time microwave moisture measurement sensors at the exit of all eight aggregate bins and in each mixer to sense moisture variation and compensate accordingly. With concrete cored brick, concrete coloured tumbled walling and coloured concrete block paving in mind, a Wurschum 4 “big bag” colour pigment dosing system was fitted. This allows pigment to be blended and blown to any one of the three Teka mixers, supplied by Conspare with a full set of concrete dosing hoppers and metering belts, delivering an extensive range of colour permutations along the feed belt to Columbia machine’s feed drawer. Three vertical cement silos were also erected local to the mixer station to convey cementitious materials to three independent weigh vessels above each mixer, to complete the batching and mixing scope.
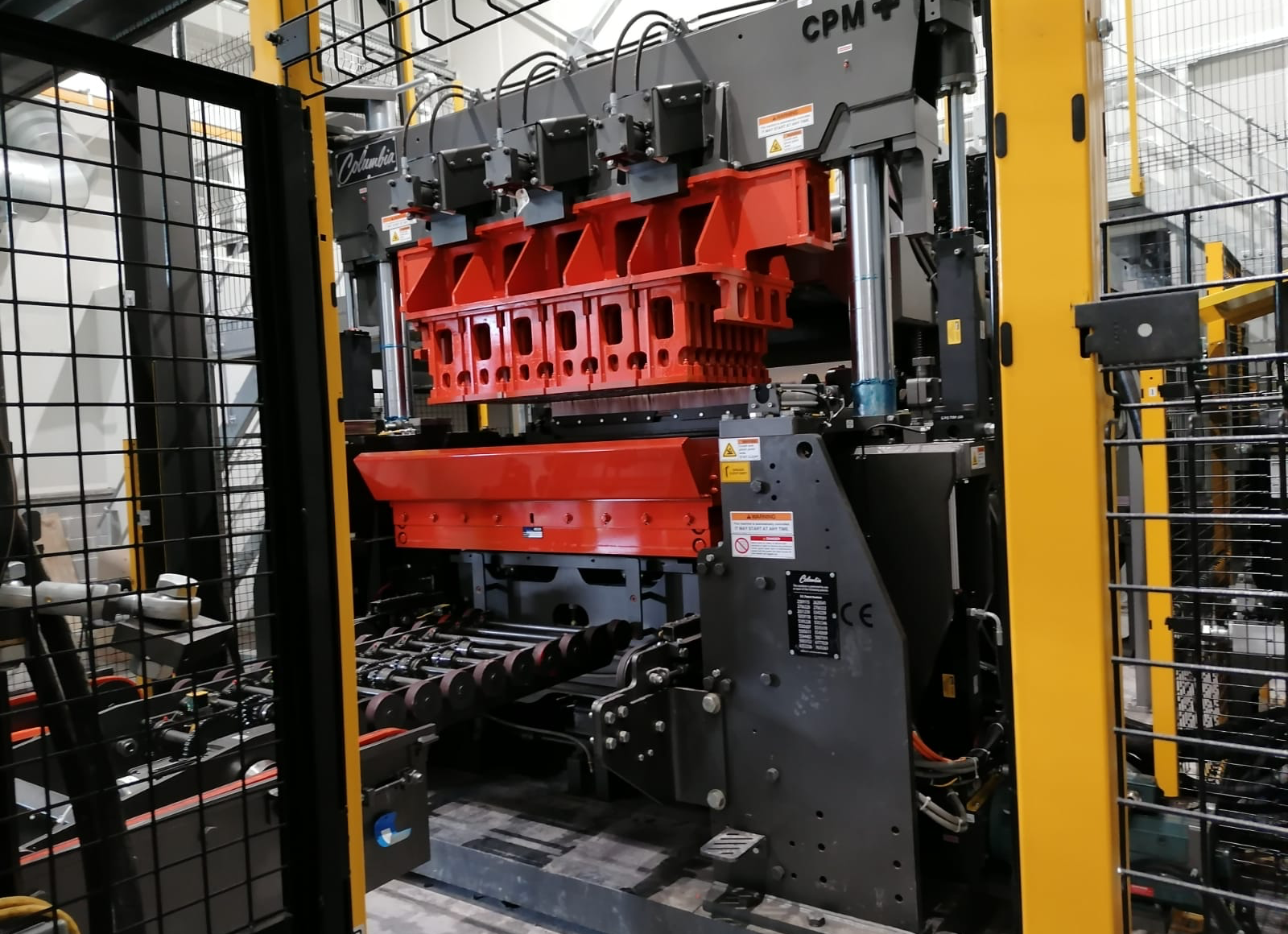
Columbia CPM+60 Concrete Products Machine for Steel Pallet 1400mm x 700mm x 15mm.
At the very heart of the new Stowell Concrete plant, the Columbia CPM+60 machine has a fl at steel production pallet size of 1400x700x15mm, chosen primarily due to the unique Columbia Vibration Technology (CVT) that provides controlled mould vibration, accurately guided in a completely vertical motion. The CVT results in longer mould life, uniform distribution of aggregates, reduced cement usage, precise product heights and product versatility. Columbia’s patented CVT combines over 80 years of innovative engineering and field-proven capability to enable the highest quality and most comprehensive range of products in the world. The CPM+60 is an easy to operate machine with user-friendly HMI/Compact Logix control and machine adjustments made from the HMI and full menu screens for quick machine set up. In changing from product to product (including any mould change requiring a height change), the machine makes the change automatically. Product change-over is recipe driven with a push-button control and tool-less agitator and strike-off plate removal.
The machine also features forced oil lubrication, a laser probe to control the feed drawer material level, full isolation between rear feed drawer section and machine centre section vibration, hydraulic linear agitation, remote valve stand, electronic product height control, product reject control and automatic mass control.
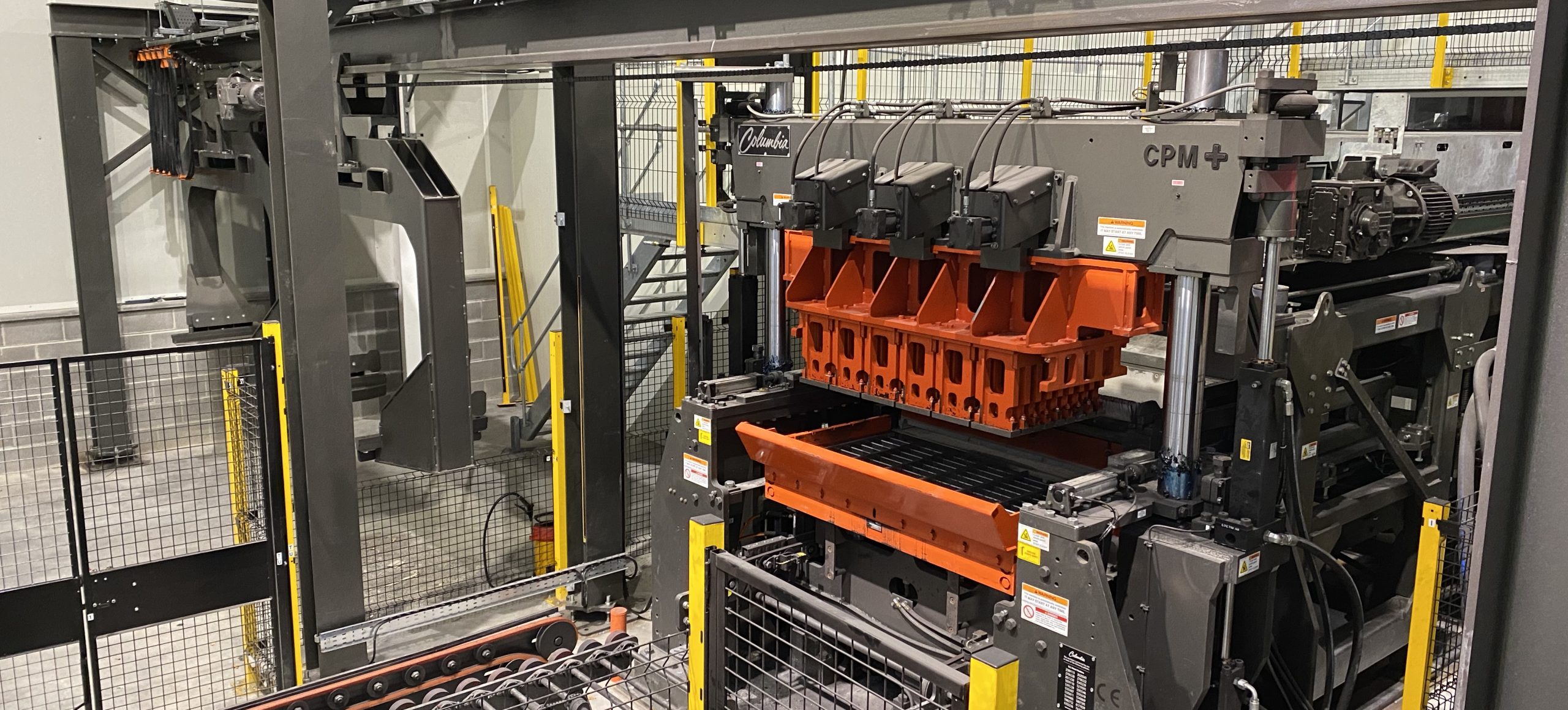
Twin Cassette Fully Automatic Mould Change Inside a Generous CDS Sound Room with 2.5 Tonne Overhead Crane and Targeted Dust Extraction.
Vince Stowell was meticulous in his plant design to include a generous sound room with separate hydraulic pump room around the CPM+60 machine. The sound room is separate from a dual-level, air-conditioned operator control room raised at first floor to 2.5 metres from the factory floor and again to a second floor at 5 metres. The operators have a fantastic view of the machine from side and front through deep panes of full height acoustic glass. An automatic dust extraction facility is included in the sound room to target the natural dust plume generated during tamping and vibration. The sound room and operator control room were designed and supplied by CDS Group.
“We believe our machine operators are the most important part of the potential 24-hour factory shift operation. We aim to raise our working conditions to the very best possible standard by minimising noise and increasing machine visibility and light to a maximum. We have also eliminated manual handling during mould changes, including easy feed drawer agitator changes by overhead crane.” explained Vince Stowell.
The 4 Tonne, Automatic Mould Change facility, was purchased with dual cassettes which run on a floor supported overhead monorail system. The first of the two cassettes is used to extract the mould from the machine while the second cassette offers a new mould. A mould change is very simply done from a menu-driven touch panel for different products and heights, and a complete mould change is performed in less than 4 minutes for products that are the same height.
Designed into the new factory building there is a dedicated mould workshop for the rebuild of genuine Columbia moulds, fully fitted out with a 3.5 Tonne overhead crane, a precision machined surface table and a specialist mould alignment fixture to allow off-line alignment of mould shoes with die cavities. Moulds are routinely inspected, oiled and stored after use and overhauled in the new workshop.
After a brush and air blast to remove debris from the fresh product, as part of a stringent quality control policy, Stowell Concrete has installed a pallet and product weight and height check facility on the green side of the plant. Every pallet of product is checked on the run for mass and height before entering the curing chamber, and a visible alarm is wired back to the control room to alert of out-of-tolerance.
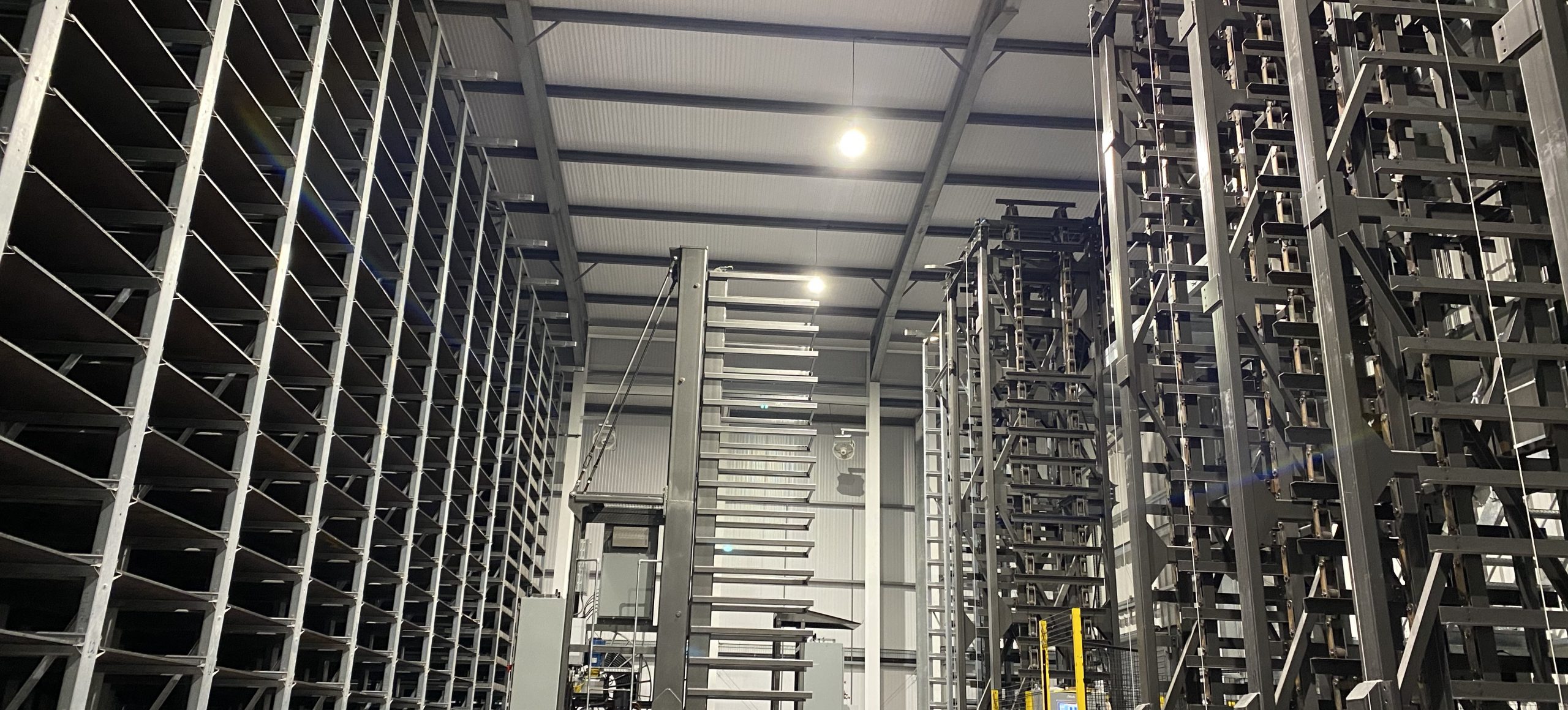
Columbia 18 Tonne PTS with Turntable, Green Side Stacker, 2 x Buffers, 2 x Dry Side Unstackers + CDS Chamber Racking System for 7,000 Pallet Capacity.
The green product is gently conveyed along smooth urethane belt conveyors to a stacker where two pallets of product per shelf are elevated to 18 shelves high and a maximum combined pallet and product payload of 18 tonnes. The load is then collected by the PTS up-car and brought onto the lo-car for turntable rotation and transport to the correct location in the fully automatic curing chamber sequence. The precise, galvanised mild steel curing chamber holds 7,000 production pallets and was supplied by CDS Group with production pallets supplied by Clarkes of Stillington. DIN standard S30 lo-car and up-car rails were carefully mitred and then staggered to ensure a smooth and gentle transition of the car wheels throughout the curing chamber.
A single atmosphere, fully temperature and humidity controlled chamber with all-round air circulation was designed and built by CDS Group, to ensure completely even curing conditions and no colour variation of those products that contain pigment. The main factory building was constructed by Rose Engineering, to an exacting standard. Local firms were used where possible with GAR contracted to complete the shed and yard foundations and Wesco Systems supplying the electrics for the site.
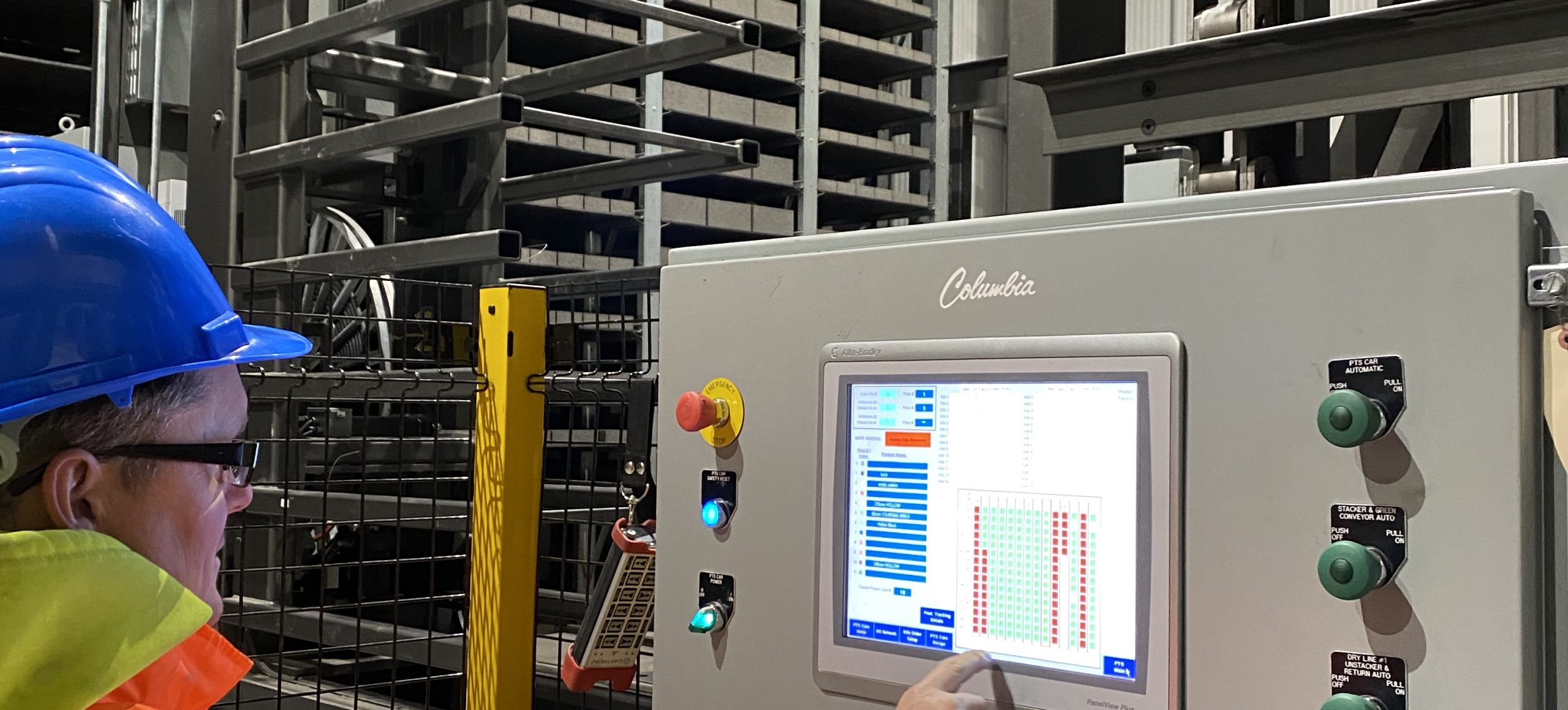
Terry Santo, Stowell Factory Manager, operating the local PTS controls from the guarded and interlocked viewing area within the temperature and humidity controlled curing chamber.
The carefully regulated single atmosphere environment in the curing chamber allows for 24-hour operation of the plant. Products can exit the chamber on two separate dry side lines, an outer line for routine fast cycle production and a second inner line for slower cure / slower cycle aged products. Not yet installed, an in-line, two-way split and “true tumble” secondary processing line is currently on order with Columbia and will be integrated into their production in autumn 2021 to increase the Stowell product range further.
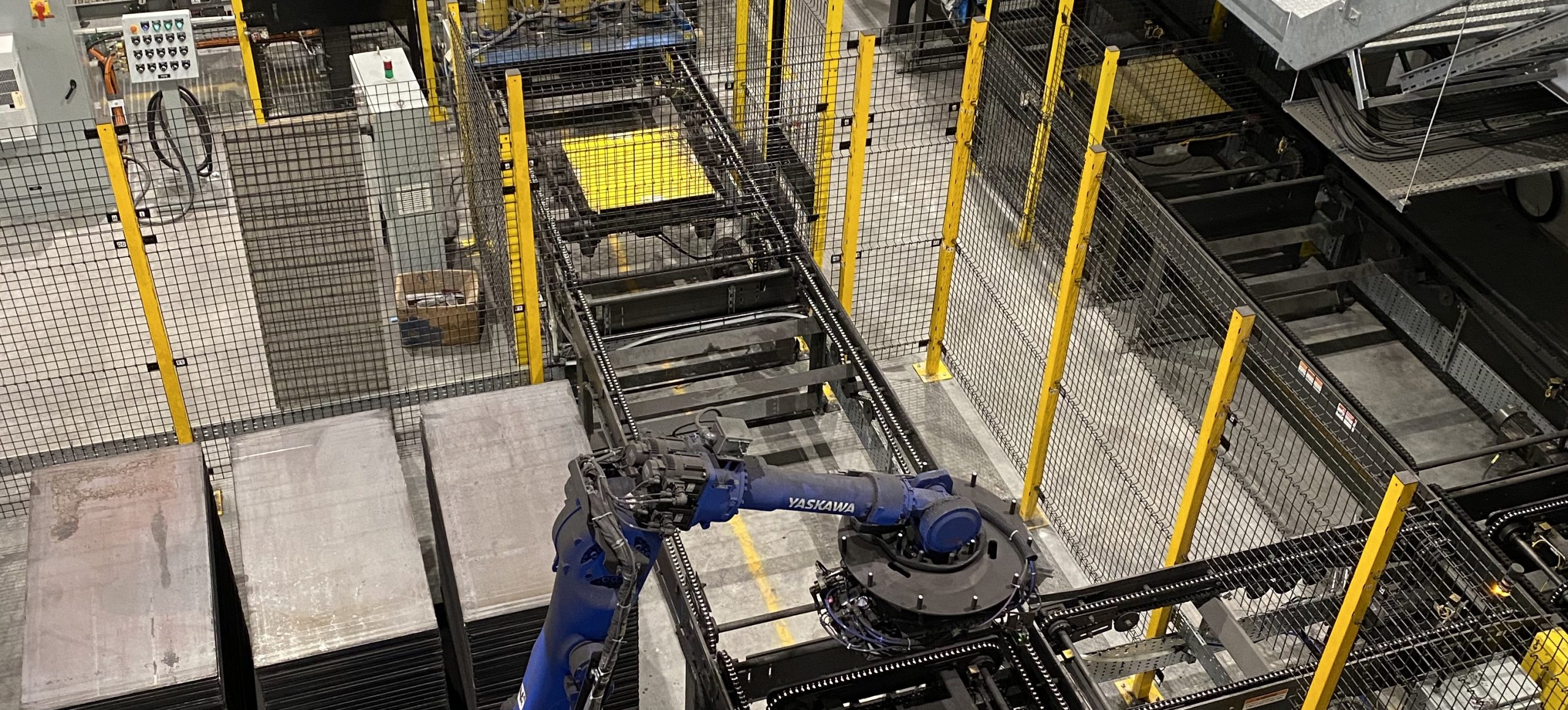
Twin Dry Side Pallet Return, Lift Blade Push-Offs, Brush, Grinding and Pallet Turn-Over to Robotic Buffer Accumulation of 510 Pallets.
Upon exiting the curing chamber on the outer dry side conveyor line, the product is removed from the production pallet by a dual set of lift-blade push-off machines.
The empty pallet is then conveyed to brushing to remove any fine debris before being turned over to even out the vibration through the production pallet on the next machine cycle.
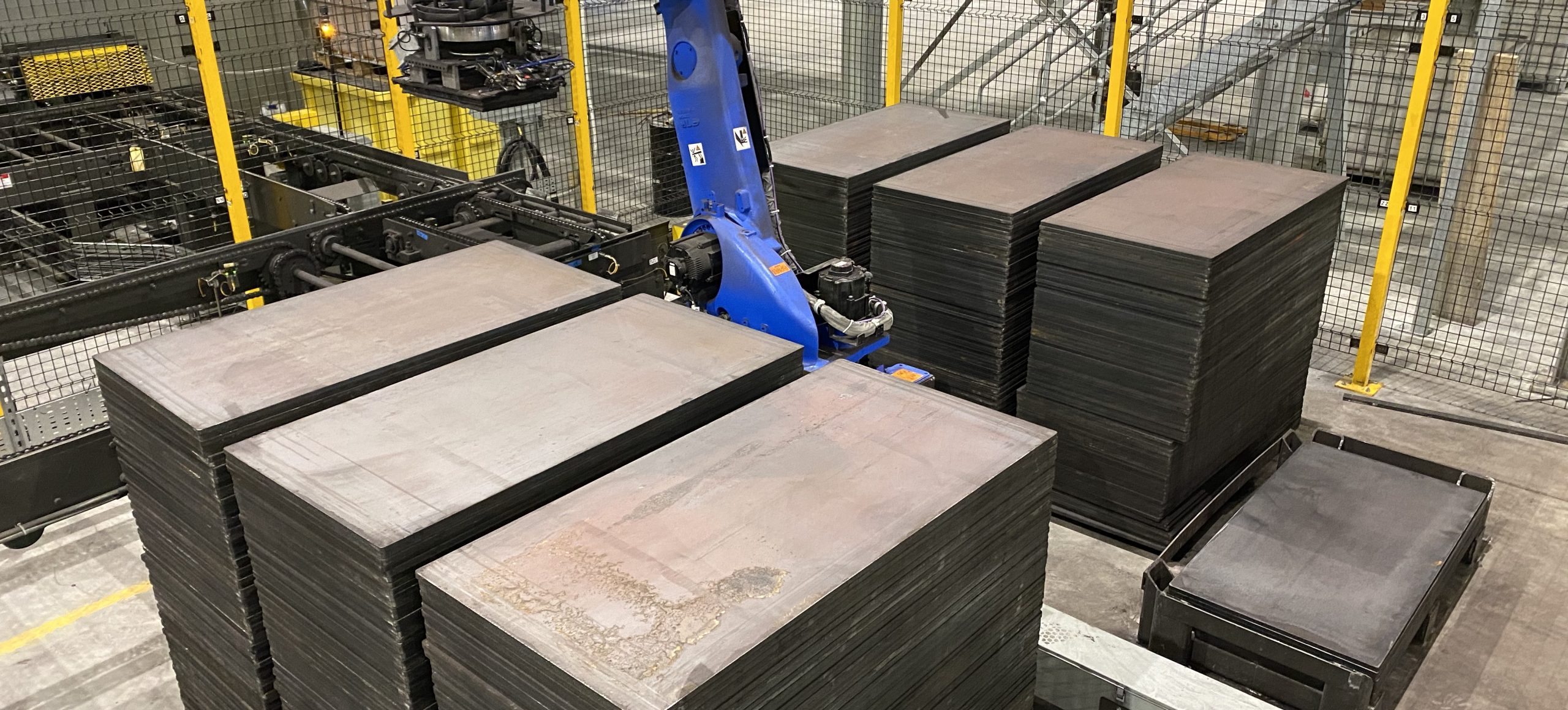
Robotic Buffer Accumulation of up to 510 Pallets.
To facilitate a degree of independent operation between the plant’s dry and green sides, a robotic pallet accumulation buffer is included on the dry side, immediately after the pallet turnover. If the CPM+60 is calling for a pallet, it is conveyed straight to the block machine. However, if it is not called for, the pallet is automatically lifted by the robot vacuum to a storage buffer until the machine signals it. Similarly, if the plant’s cubing side is stopped (perhaps for changes of strap), the block machine can continue by consuming the buffer stock via the vacuum robot. The steel pallet is finally coated with oil before re-entry to the block machine.
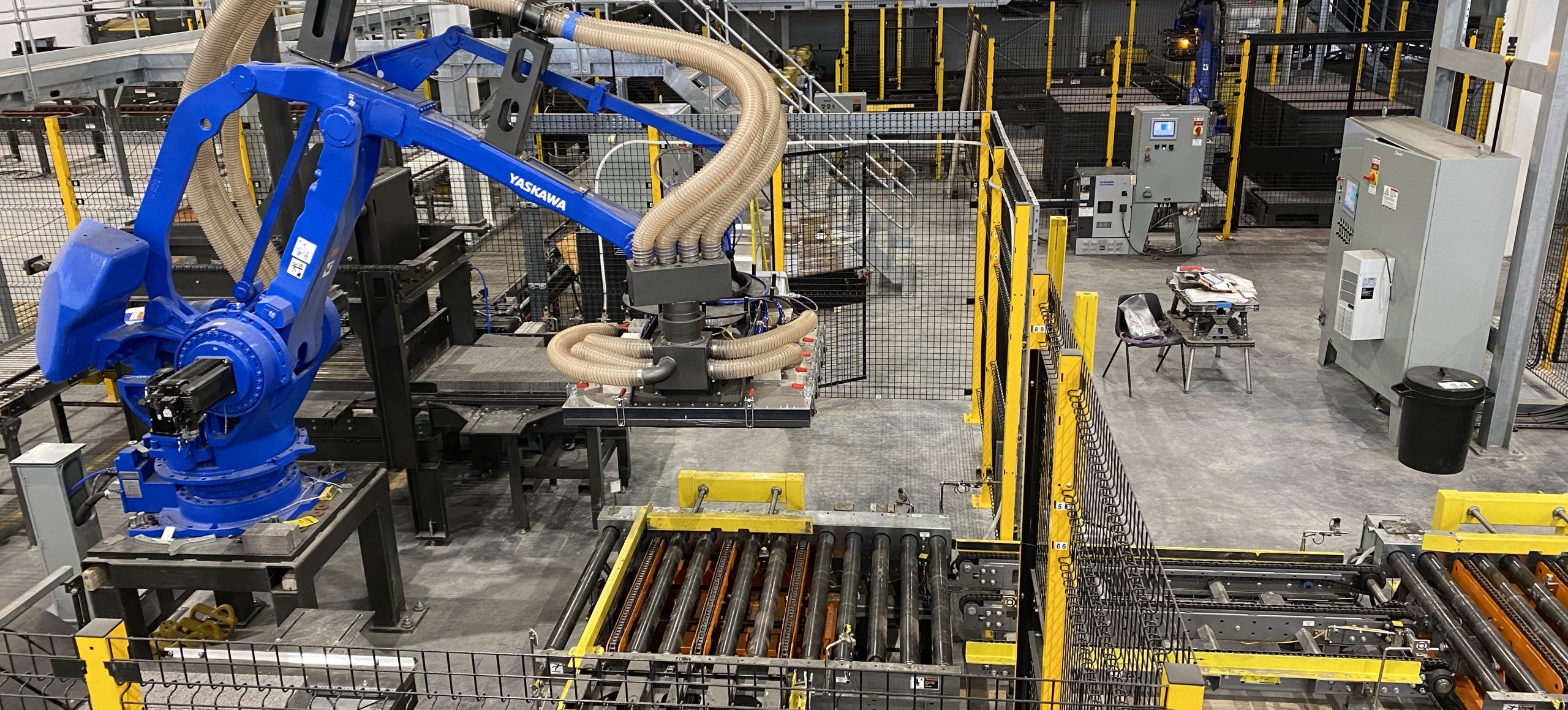
Vacuum Product Cubing Robot with Columbia Slave Pallet Strapping and Hooding Circuit.
Product is pushed from the production pallet and travels along powered midget roll conveyors to a robotic cubing system with two-row forming in-feed lines. A Yaskawa MPL robotic arm with vacuum end effector and dedicated foam surface pick pan is used to lift from both pick points and place each tier of product in the final cube.
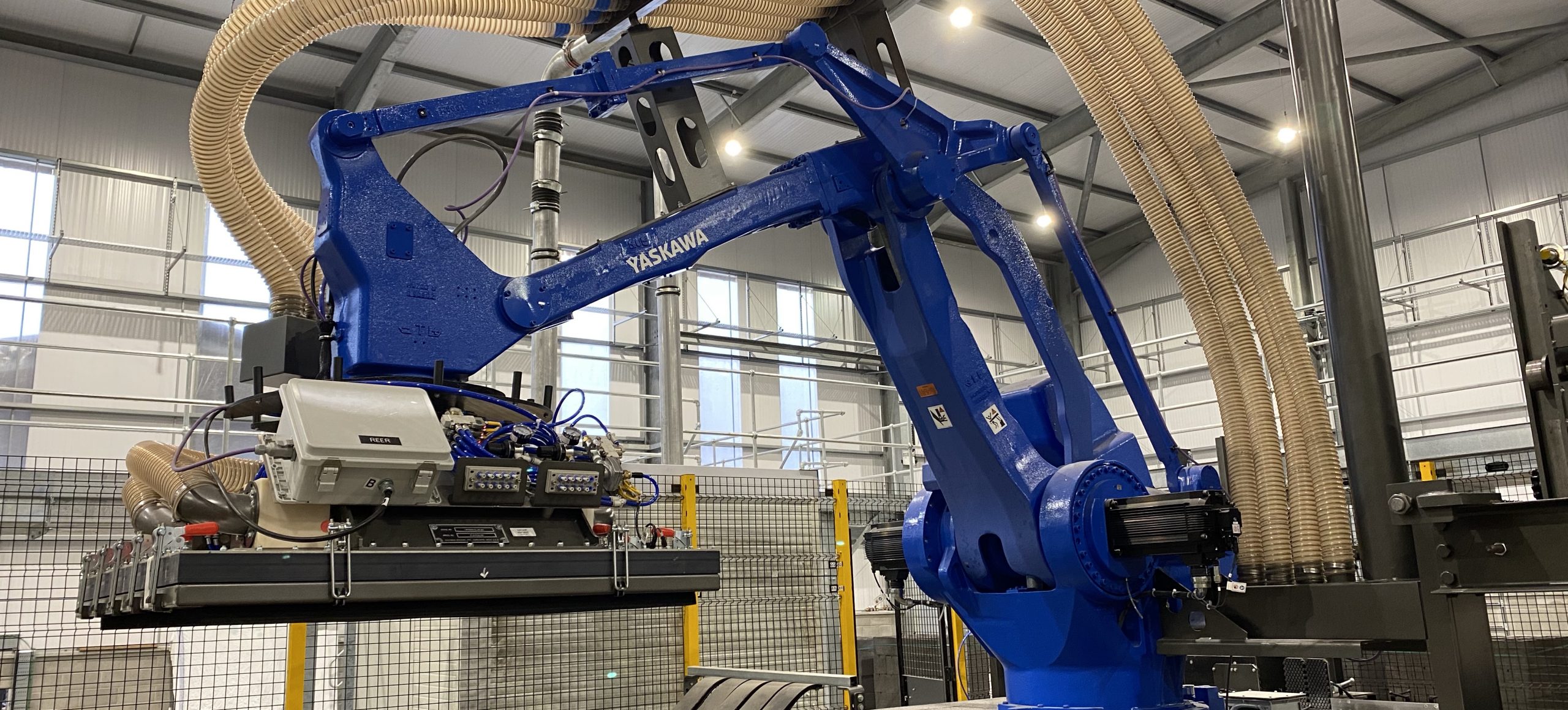
Yaskawa robotic arm cuber, vacuum end effector and dedicated foam surface pick pan.
Each cube of product is built onto a specialist metal slave pallet, designed to allow vertical straps to be threaded through the metal pallet on the underside of the cube in two directions. The conveyor loop system contains approximately 30 slave pallets which circulate continuously and can work with or without a wooden transport pallet as required and depending on customer preference. The full cubing slave circuit consists of two vertical and two horizontal OMS strappers; an OMS stretch plastic fi lm hooding machine and two gantry style wood pallet dispensers.
The foundation and building infrastructure are already in place for a second phase CPM+60 plant and another Columbia 18 Tonne PTS system.
“We would like to extend our sincere thanks to the entire Stowell team for investing in a long-term partnership with Columbia and for their support throughout the Phase 1 project. We wish the business continued rapid growth with their exciting new product range, and we very much look forward to Phase 2 and the installation of our splitting and ageing equipment in 2021,” said Kevin Brown, Columbia Machine Division President.

The first of two sets of horizontal and vertical OMS strapping machines.
<h5>The second of two horizontal and vertical OMS strapping machines in the Columbia automatic cube strapping and stretch plastic film hooding line.</h5>
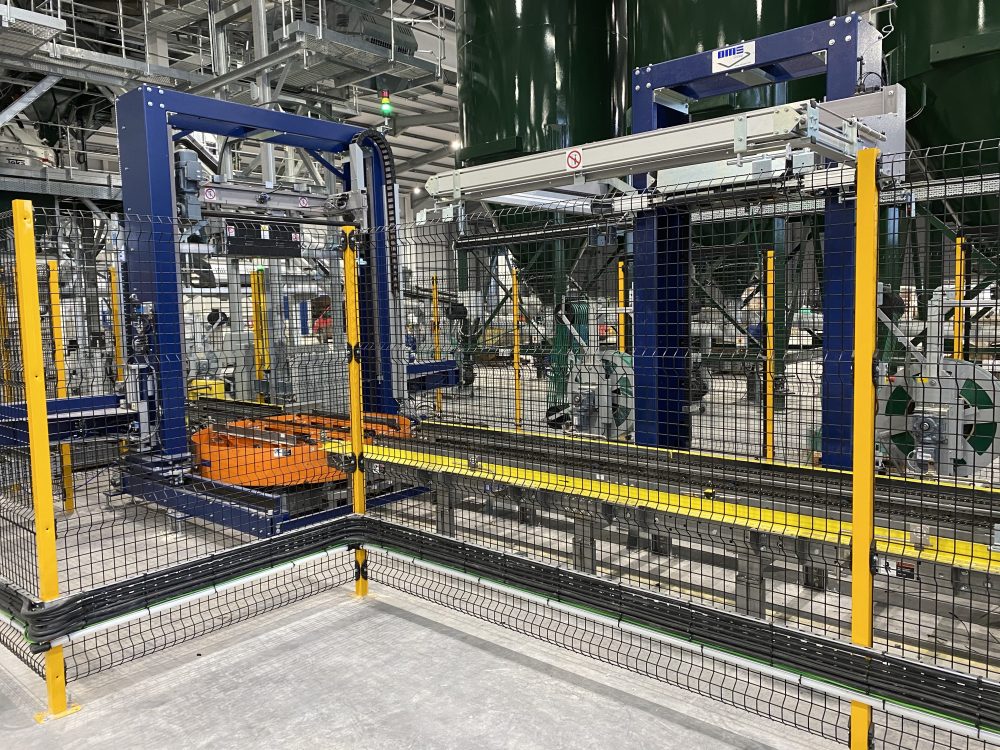
<h5>First run of UK concrete coursing brick leaving the Stowell CPM+60 machine.</h5>
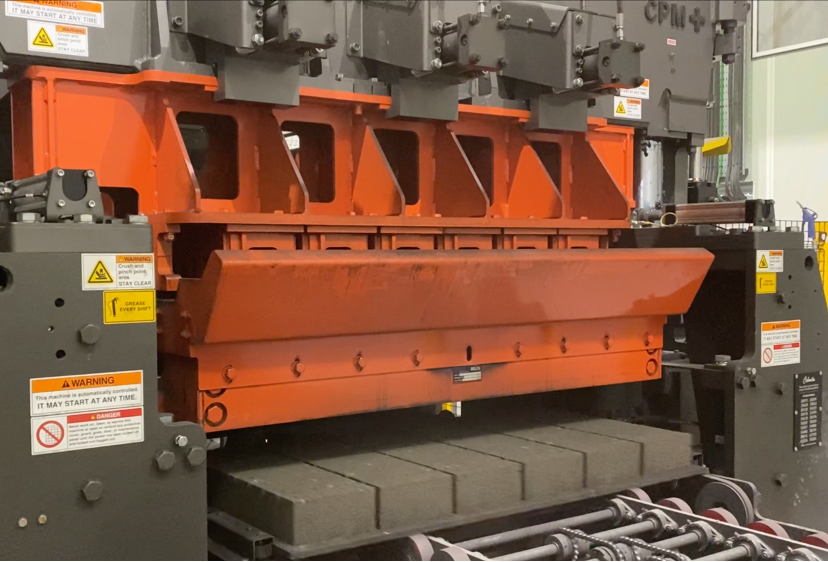
<h5>First cubes of UK concrete coursing brick passing through the strapping line.</h5>
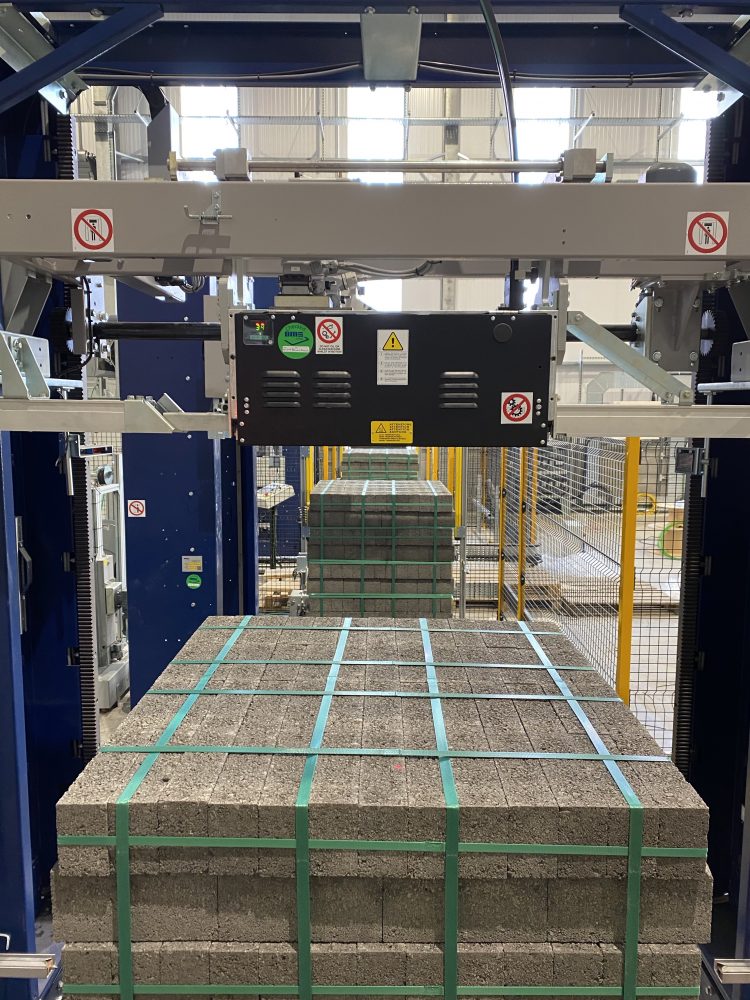
<h5>A cube of voided UK concrete coursing brick (with horizontal and two side vertical strapping) leaves the Stowell strapping line on a slave strapping pallet.</h5>
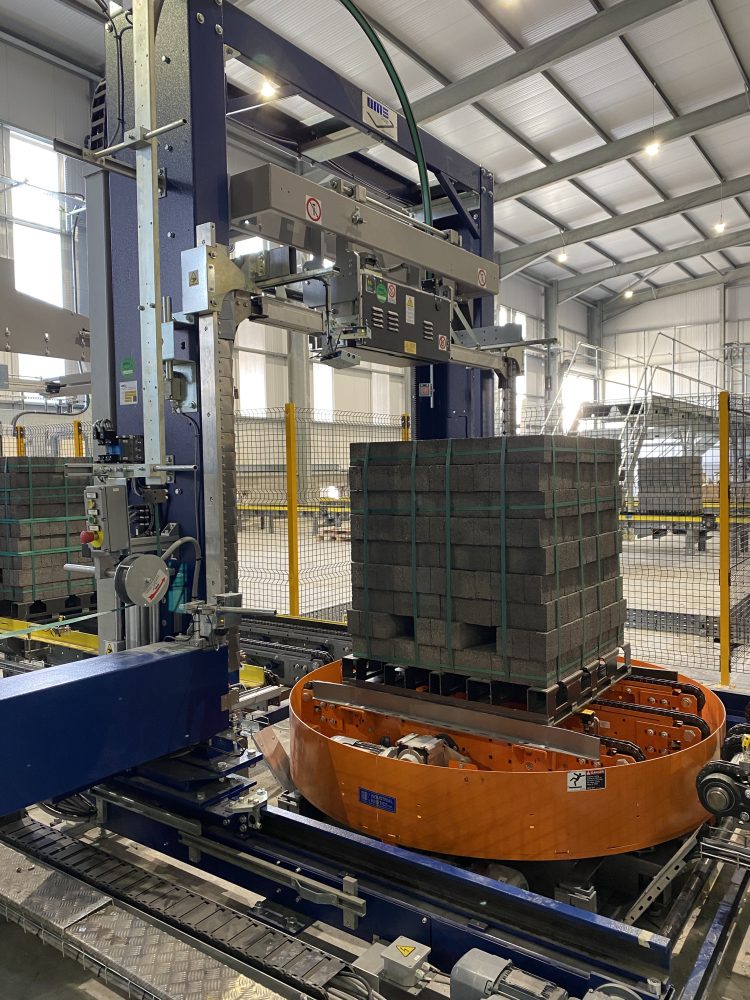
<h5>A strapped cube of UK concrete coursing brick ready to receive a plastic stretch film cover.</h5>
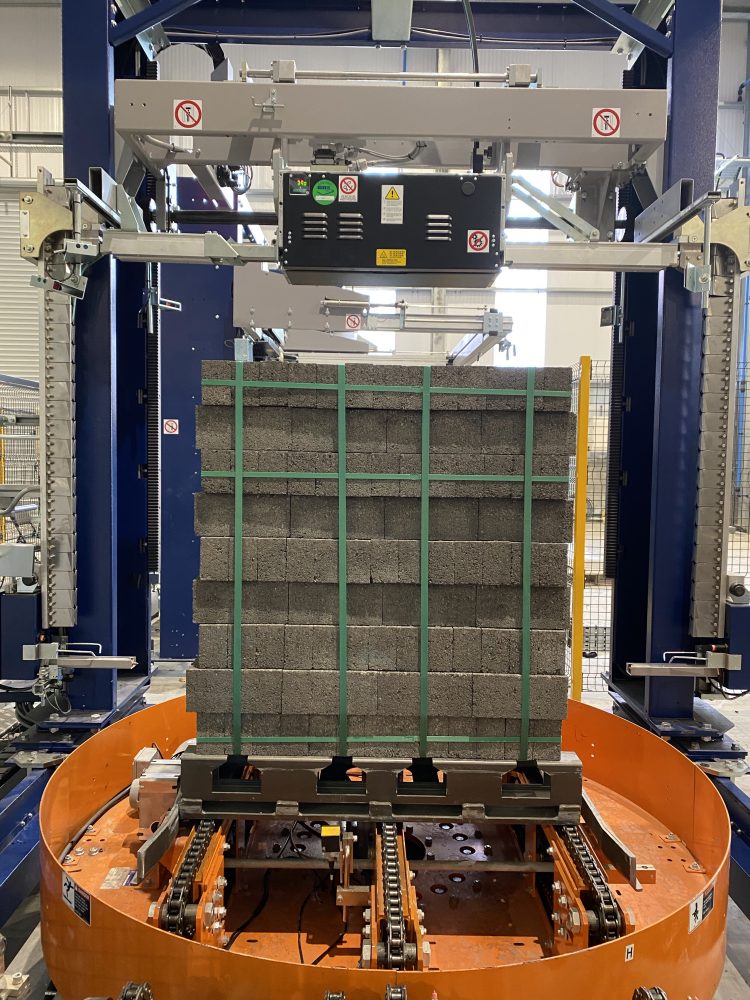
<h5>Stretch hooding machinery automatically fits a plastic stretch film cover over final cube.</h5>
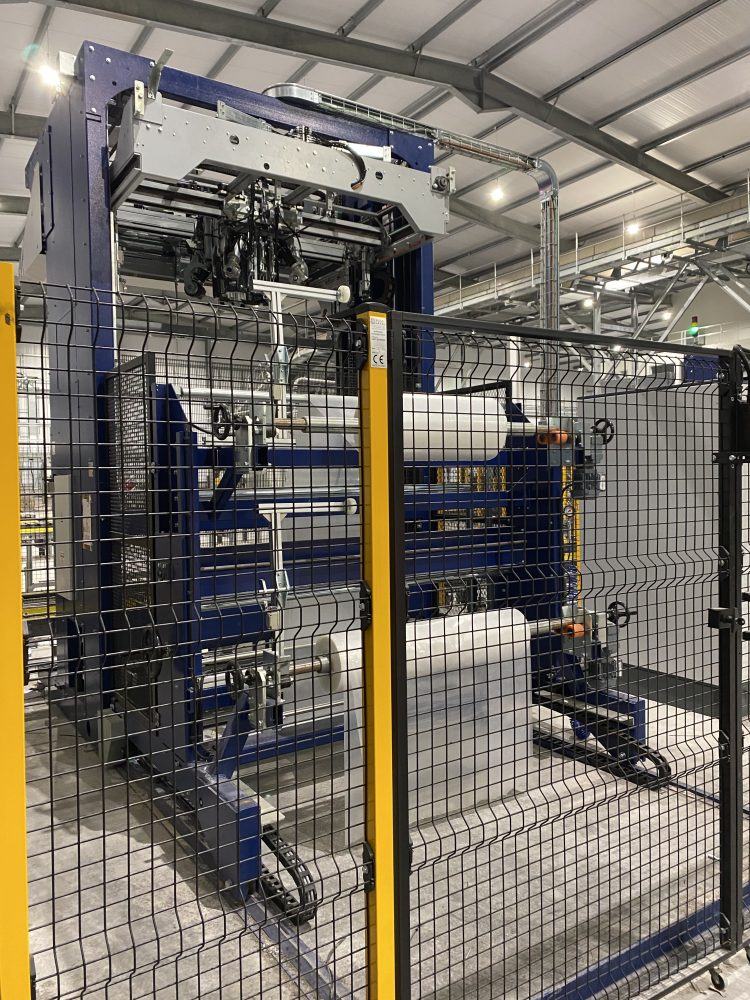