Robotic Solutions Advance Concrete Production
Columbia continues to investigate and develop new technologies, products, and programming to enhance and improve the operator experience and increase equipment reliability and performance handling for concrete products of all shapes and sizes.
Columbia Machine, Inc. has a long history of creating advanced products that provide exceptional value in concrete product production.
Its journey into robotics started with a joint venture in robotic palletizing with Okura Yusoki Co., Ltd. in 1996. Strong technical history from Okura and palletizing expertise from Columbia Machine are the foundation of Columbia/Okura LLC, allowing it to fulfill application requirements of unique problems across multiple industries. Its robotic palletizers, capable of supporting niches requirements, compliment Columbia Machine’s already successful lines of conventional palletizers.
In concrete production facilities, robots operate in harsh environments. They contend with heavy loads, versatile handling requirements, a wide range of operator experience, low maintenance expectations, highly robust design expectations, and rigorous production schedules. Applications that benefit from robotics solutions are Cubing (clamp and vacuum), pallet buffering, offline value-added processing, and product handling. Similarly, robots can handle heavy loads, repetitive motions, and unique space constraints.
Robots can handle products individually, in rows, and full layers, as well as manage tier courses and product arranging. They can be integrated into an existing system or stand alone as a wholly robotic or hybrid cubing system with a slide deck that aids in arranging and cubing products.
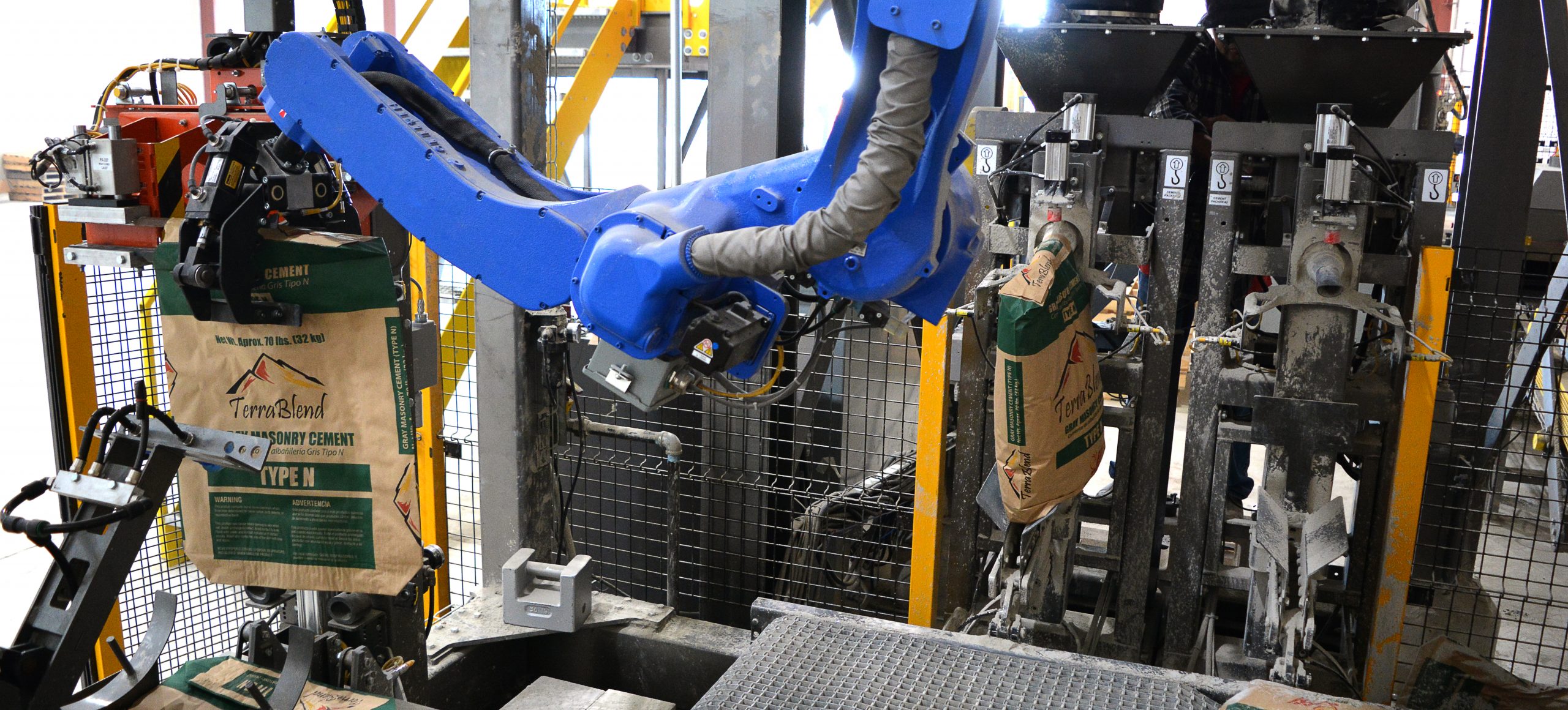
When cubing concrete products, robotic vacuum and clamp-type end effectors are well-suited to simple and complex layer patterns.
For example, pavers, slabs, and other products of lower height or solid faces commonly use vacuum end effectors. Generally, the vacuum is a dedicated high-flow system located near the robot.
Clamp end effectors that use pneumatic cylinders or electric actuators may be required when product heights get above 100mm/4”, if products are too porous to achieve proper suction, or if not enough horizontal concrete area is available to lift the load. In either case, robotic cubing adds the versatility producers require, reducing sliding actions as well as face and vertical wall scraping while handling products gently.
In 1998, Columbia Machine ventured into robotic applications for the concrete products industry with an installation at Oberfield’s Inc. in Columbus, Ohio. Oberfield’s system uses a vacuum type end effector and handles its vast array of standard products. The robots receive yearly maintenance and continue to perform well, even with the implementation of additional capabilities that serve to address product mix changes throughout the years.
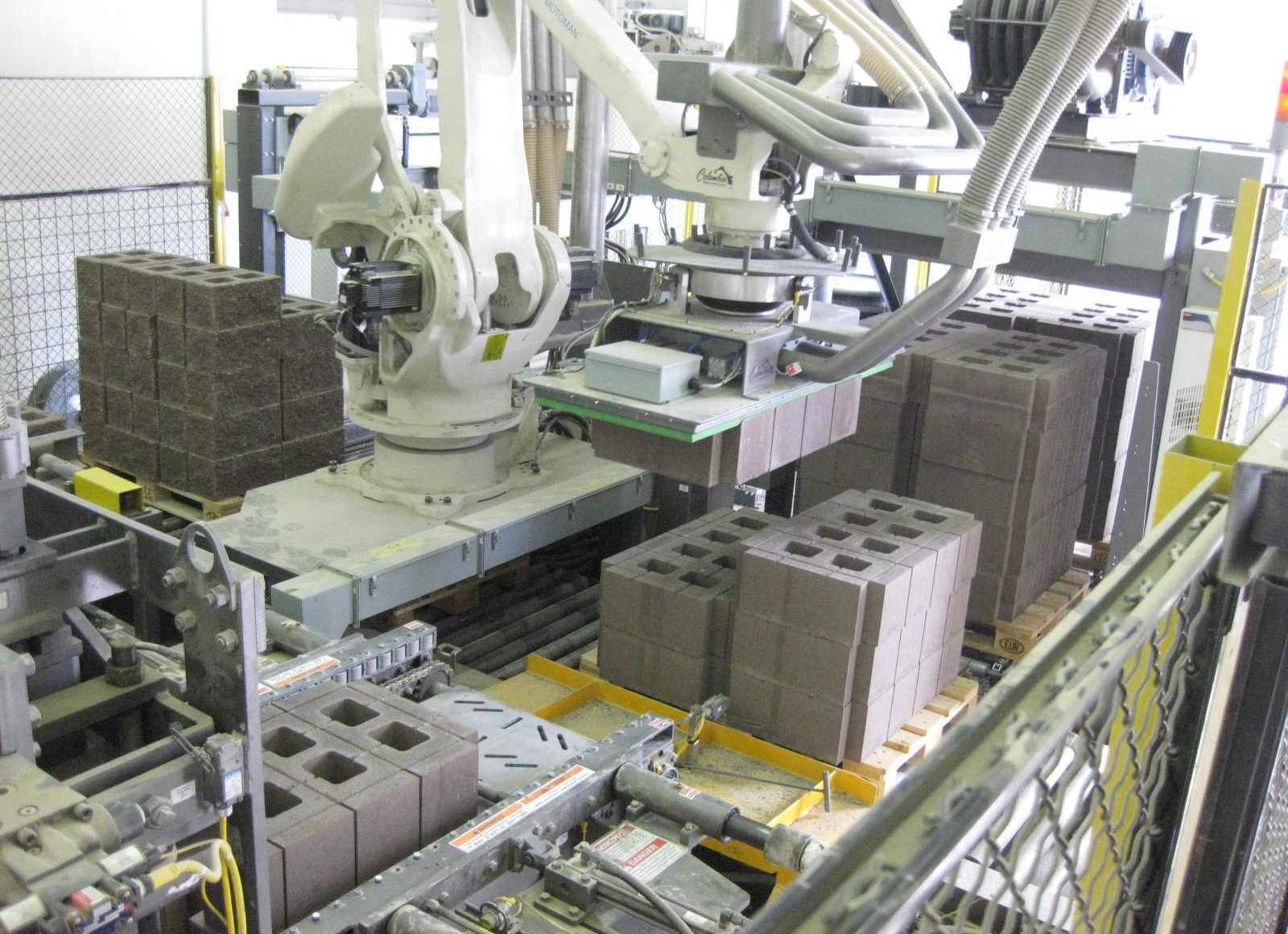
Pallet buffering, where empty production pallets are pulled out of the production loop temporarily, is frequently used in production facilities.
This type of system allows the cubing and dry product lines to operate nearly independent of the concrete forming machine. By supplying a steady flow of pallets to the concrete forming machine, regulated cycle rates enable variation in cubing and product making cycle rates, preventing plant downtime when issues arise.
Columbia systems remove a pallet and place it in one of six stationary stacks (600-900 pallets total) and, if desired, can turn the pallet over in the process. This system uses compressed air powered vacuum generators mounted to suction cups operated using compressed air. Integrated conveyance systems allow for the storage of substantial quantities of pallets, increasing ballet buffering potential. With these systems, adding and removing pallets can be automated. Since 2008, a Columbia customer in the UK has been operating a 600 pallet system that runs 1400mm x 700mm pallets for close to a decade.
Robots shine when it comes to value-added processing, increasing growing plants’ capabilities significantly.
De-cubing, processing, and re-cubing products that go through value-added processes allow better attention to quality and inspection, moves operators away from dust, noise, and moving equipment, and with fewer exposed moving parts can increase the time between scheduled maintenances.
Quality assurance improves when de-cubing, processing, and re-cubing products that go through value-added processes that move operators away from dust, noise, and moving equipment. Additionally, these systems have less exposed parts, increasing the time between scheduled maintenance and streamlining production.
In proper arrangements with adequate space, one robot can handle both the de-cubing and re-cubing operations.
One value-added system in the Czech Republic, installed in 2008, is an excellent example of this. Operated by one person, its system can manage offline splitting operation, is capable of taking cubes loaded into the system, splitting products in two directions, and reassembling the cube. It integrates with horizontal and vertical strapping, split debris management, vacuum debris management, wood pallet recycling, and only requires perimeter guarding.
Columbia has developed technologies specific to handling concrete products that maximize uptime with robotic applications. Its crash detection end-effector mounts allow for damage-free product pick and place while maintaining a rigid system during the move between pick and place, reducing the potential for damage or manual errors. Columbia’s vacuum brake valves to prevent high vacuum levels from damaging equipment while its custom vacuum valves allowing for fast response, high flow, and minimal vacuum loss during operation. Additionally, Columbia has universal and dedicated vacuum end effectors with multiple chambers and quick changeover, as well as clamping arms and surfaces to ensure a secure grip with product size and texture differences over a wide range of clamping sizes.
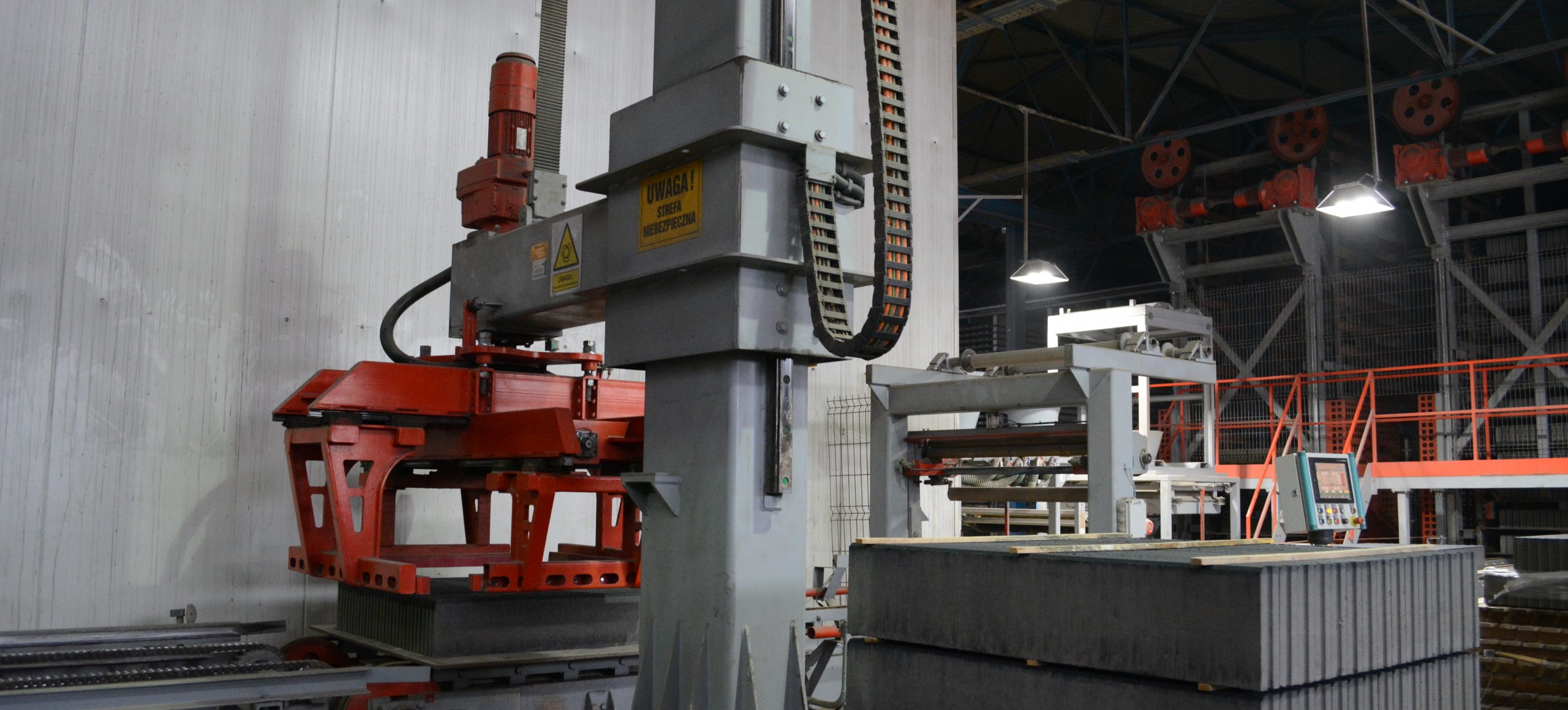
Columbia continues to investigate and develop new technologies, products, and programming to enhance and improve the operator experience and increase equipment reliability and performance handling for concrete products of all shapes and sizes. Continued investment into the robotic applications for the concrete products industry means long-term advancements in technologies and equipment that will support customers’ requirements to deliver on-time, exceed expectations and maintain competitive prices.
Written by Stacy Gildersleeve, PE, Chief Engineer
Columbia Machine, Inc.