The CPM+ line, updated now for your needs tomorrow
Columbia Machine, Inc. launched the CPM+ series of block machines in 2016 and was quick to deliver nearly a dozen machines over approximately 18 months. This updated version of the already popular and highly successful CPM series was revamped to include lots of features geared towards the needs of producers to boost its already legendary reputation for versatility, ruggedness, efficiency, and cement savings. Easy-to-operate, recipe-driven, very fast mold change, no tool height changes, and intuitive HMI screens were all goals of the new design. Based on demand, it appears to be a success.
CVT is at the core of every Columbia concrete products machine. Columbia Vibration Technology includes features such as vertical mechanical vibration, critically damped and adaptable four-way variable pressure air sprung pallet table, variable force air-stroke actuated compression beam force, rugged mechanical height stops, robust and programmable stripping action, and a vibration isolated heavy mass center section.
A wide range of high-quality products is what you can expect, every hour, every shift, all year long. Every CPM is capable of making industry leading compressive strength pavers, height accurate retaining wall and other dry stacked products, the thinnest face shells required on CMUs, beautifully colored capped and color blended products as well as the wide range of specialty horizontally cored, restricted fill and even large snipe curbstone products.
The Center Section of the CPM+ series, mounted on engineered isolators resting on its own foundation, is designed to concentrate the vibration energy where it is most useful, into the mold that compacts the material that makes your products. This purposefully heavy section is the workhorse of the CPM+ machine, constructed of heavy duty frame and beams, powered by industrial strength hydraulics, pneumatics, and electric drives.
The Feed Drawer Section, rigidly anchored to its own foundation, provides a stable platform for the Feed Drawer to ride on. The heights of the Feed Drawer supports are recipe driven to a precision height that creates very repeatable material heights from cycle-to-cycle and mold-to-mold. Laser material height measurement ensures high accuracy and repeatability of material levels in the Feed Drawer for every cycle.
The Feed Drawer carries material over the mold during the fill cycle while a variable speed linear agitator oscillates a universal or custom designed agitator to properly distribute material into precision mold cavities. The Feed Drawer comes equipped with a lifting Strike-off to reduce material spillage during the forward motion of the drawer and your choice of multiple wiper and brush designs to keep the mold shoes clean during production. The material is usually fed into the Feed Drawer using an overhead Meter Feed Belt to keep material light, fluffy, and flowable.
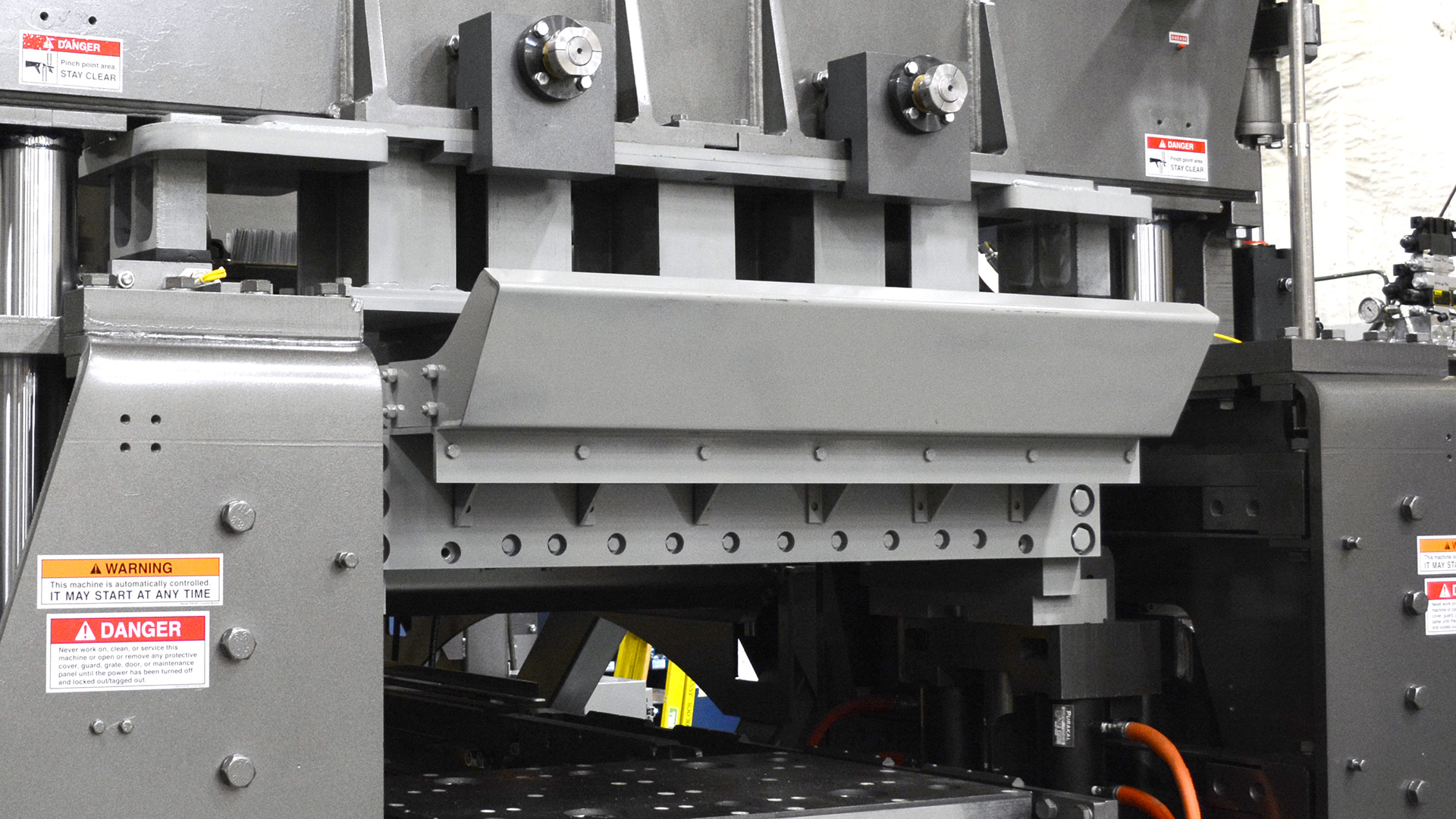
Pallet Feed is accomplished by moving empty pallets through the machine fast while transferring out green products gently. Empty pallets can be fed into the machine from the rear or either side, providing versatility to place the machine as needed to match building and production requirements. The machine is configured at the time of order for steel or composite pallets to accommodate your preference.
Mold Extraction and Exchange is completely automatic, hands-free, and requires no tools or entering the guarding. The pin aligned, hydraulically clamped mold box and pre-aligned, mechanically clamped mold head provide fast and robust attachment of the mold components to the machine while also providing drastically reduced mold change times. Sub ten-minute mold changes are common when only using the extractor, below seven minutes is achievable when using the optional mold exchange system, and below 5 minutes has been known to happen.
Recipe control is provided from an intuitive HMI with screens developed to reduce searching for what your operator needs. Need to adjust a setting of the Vibrator? Simply tap the Vibrator on the screen. Want to adjust a setting of the Feed Drawer? Just tap the Feed Drawer on the screen. All the settings you need can be found by using the on-screen graphics or by using the machine function specific tabs.
When something does need to be found regarding an alarm, error, failed switch, I/O error, or other electrical issues. Debugging time is reduced due to the ability to trace things down using the HMI. Wire numbers, I/O locations, physical switch locations, etc. are all accessible right on the HMI, reducing the need to track down electrical schematics.
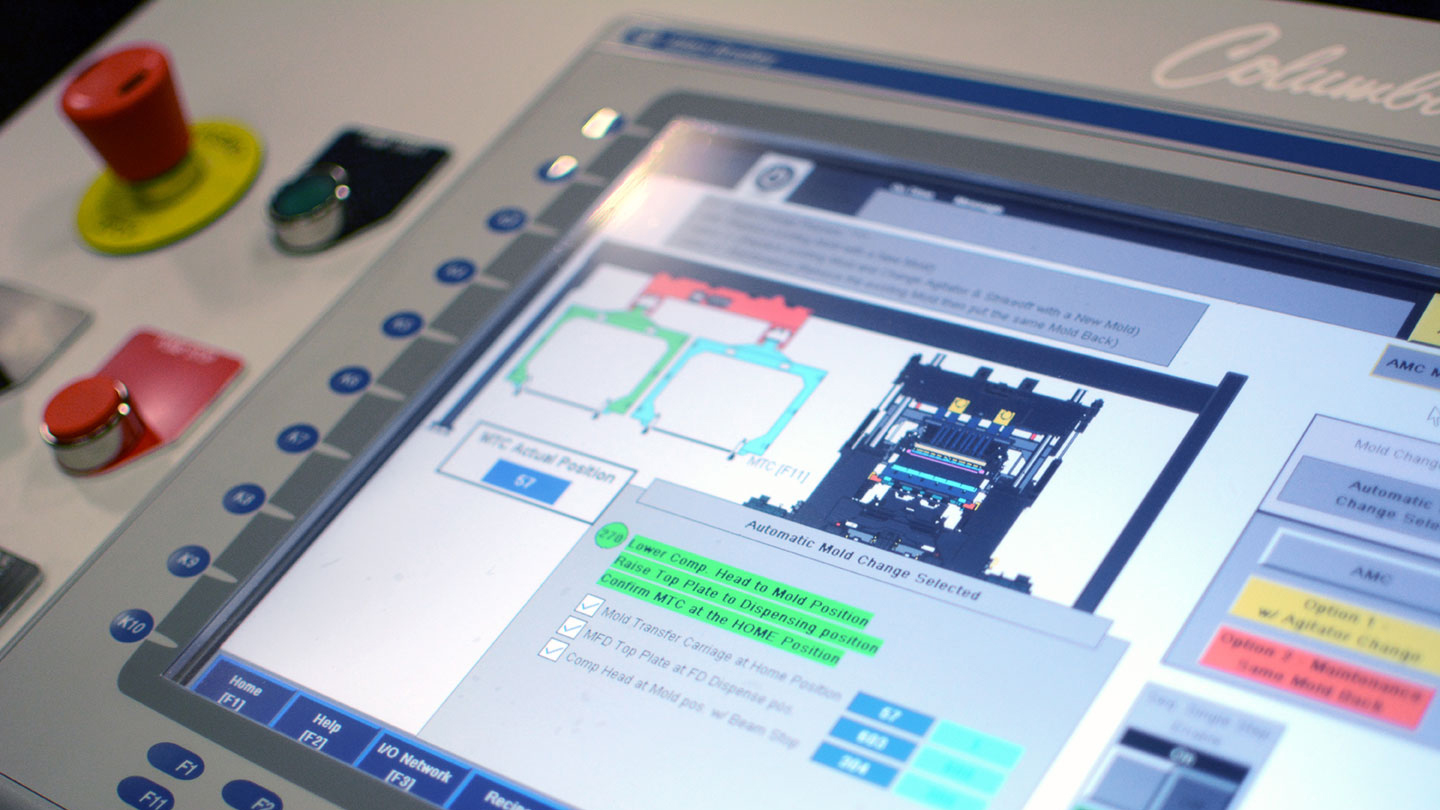
With the use of Command View, production reporting is made easy. In addition, online support is possible so a Columbia service technician or engineer can log in remotely and monitor your machine with you. The available Command View PC that is connected to the CPM+ block machine comes with all the software you need to not only access your machine program but can be loaded with other software your operators might need. If you have multiple Command View compatible machines such as a Cuber, PTS or other equipment, they can all be connected and viewed from one.
All hydraulic, pneumatic, position, pressure and vibration controls needed to optimize production are adjustable from the HMI and saved in the library of recipes. Recipe settings can be reviewed and updated while the machine is operating, allowing for temporary adjustments for subtle changes in concrete properties or other production variables. Rugged and industry tested components are used throughout the system. Pumps, valves, cylinders, hoses, fittings, and filtration have all passed the test in plants throughout the world.
Hydraulic pump units for machine motion and vibrator lubrication are designed, manufactured and tested by Columbia to the specific needs of the machine and your local temperature ranges. Designed to withstand the contaminated environment commonly found in block plants around the world, the reliability of hydraulic power is key to machine uptime; proper filtration and cooling are provided with every hydraulic pump unit to keep things reliable.
Electric, pneumatic and hydraulic control devices are located in two central areas of the machine to assist in access requirements for troubleshooting and maintenance. All hydraulic valve and manifold locations include integrated drip trays with drain hoses, reducing the likelihood of contamination making it into concrete or onto other areas of the equipment.
Electric, pneumatic and hydraulic cords, cables, and hoses are all routed to keep them off the floor and out of harm’s way when inspection, maintenance or clean up around the machine is needed.
The list of features and improvements included with the CPM+ machines are geared towards the needs of producers in the ever-changing landscape of concrete products. Columbia strives to continuously improve its solutions in support of the industry, allowing the expansion of what can be offered to satisfy the end users of concrete products. Versatile, rugged, and efficient machinery to help you pave, retain, and build.
Written by Stacy Gildersleeve, Chief Engineer
August 2018